End mills are used for producing precision shapes and holes on a Milling or Turning machine. The correct selection and use of end milling cutters is paramount with either machining centers or lathes. End mills are available in a variety of design styles and materials.
Titanium coated end mills are available for extended tool life requirements. The successful application of end milling depends on how well the tool is held (supported) by the tool holder. To achieve best results an end mill must be mounted concentric in a tool holder. The end mill can be selected for the following basic processes:
- FACE MILLING - For small face areas, of relatively
shallow depth of cut. The surface finish produced can be
'scratchy".
- KEYWAY PRODUCTION - Normally two separate end mills are
required to produce a quality keyway.
- WOODRUFF KEYWAYS - Normally produced with a single
cutter, in a straight plunge operation.
- SPECIALTY CUTTING - Includes milling of tapered
surfaces, 'T" shaped slots & dovetail production.
- FINISH PROFILING - To finish the inside/outside shape on
a part with a parallel side wall.
- CAVITY DIE WORK - Generally involves plunging and finish
cutting of pockets in die steel. Cavity work requires the
production of three dimensional shapes. A Ball type End mill
is used for the finishing cutter with this application.
TYPES OF MILLING PROCEDURES
End Milling |
|
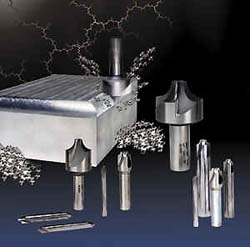 |
|
Metal removal
process that is achieved by feeding a workpiece
into a revolving cutter. The cutter will remove
material as chips. |
| | |
Conventional Milling |
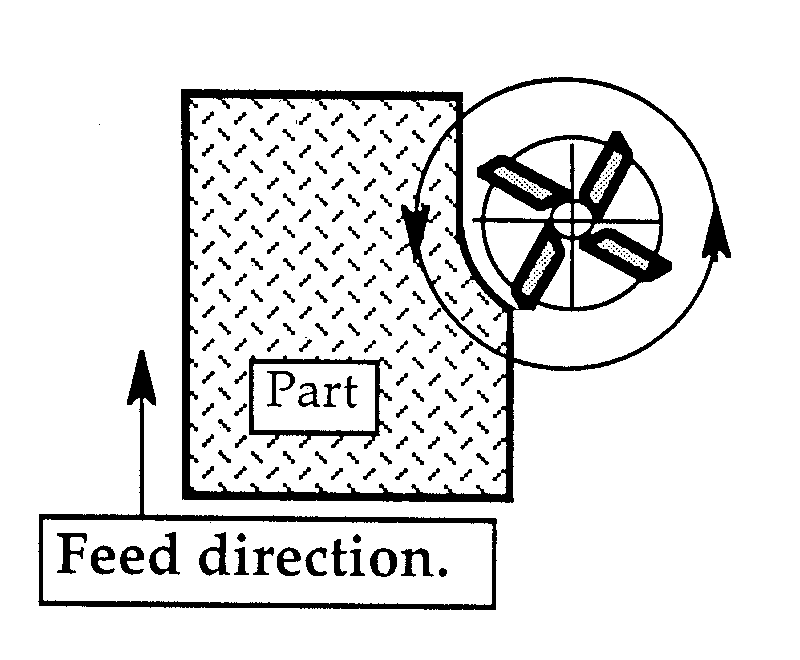 |
|
Cutter direction for
a milling operation. The cutter tending to push
the workpiece away from the part, increasing the
required feeding force. First choice for manual
machining. Sometimes called up milling.
|
| | |
Climb Milling |
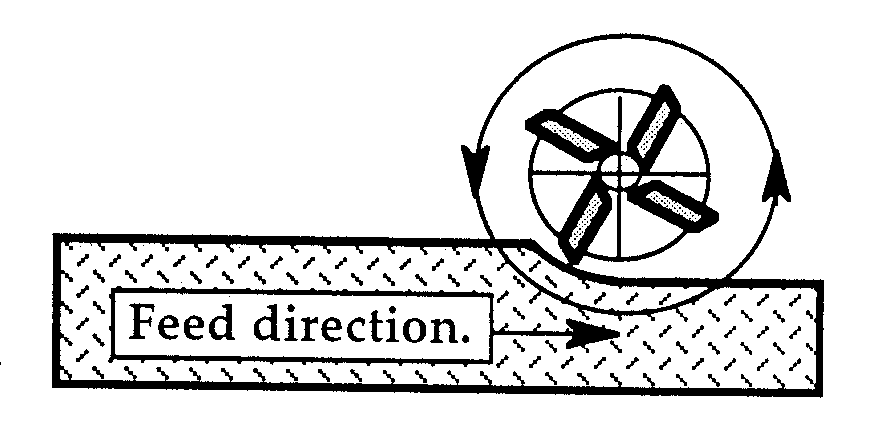 |
|
Cutter direction for
a milling operation. The cutter tends to "climb"
into the workpiece which relieves feed force
requirements. First choice for CNC machining.
Increases cutter tool life. Sometimes called
down milling. |
| | |
Ramp Cut |
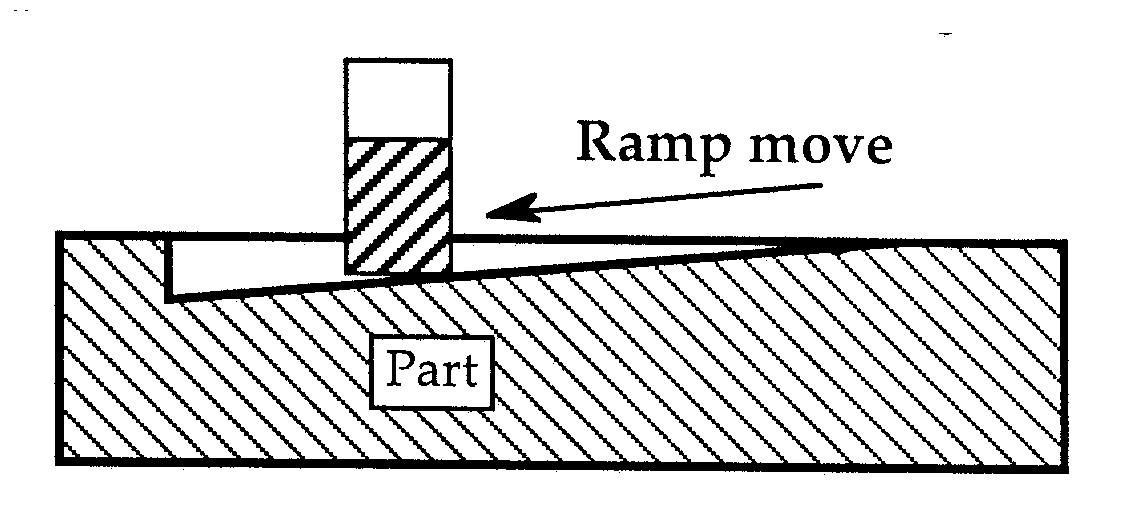 |
|
Axial feeding into a
part. CNC machine movement in the Z axis
direction and an additional axis ( X or Y ).
Angled plunging into the face of a part, feeding
in other than an axial direction. Requires a
center cutting End mill. Ramp cutting will
assist the end mill into entering into a part
face. |
| | |
Plunge Cutting |
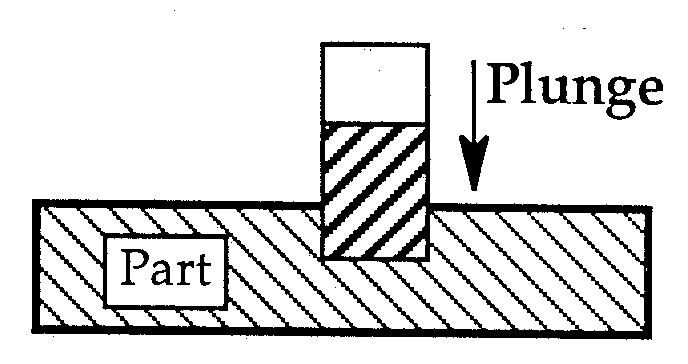 |
|
Axial feeding into a
part. CNC machine movement in the Z-axis
direction. Direct plunging into the face of a
part. Plunge feeding in a axial direction.
Requires a center cutting end mill.
|
| | |
Peripheral Milling |
|
The machining of an
edge surface of a part. Peripheral milling is
accomplished by presenting the workpiece to the
circumference or the periphery of the milling
cutter. |
| | |
|
|
« Back to training menu page |